I created the Lavergne Management Matrix to make it possible to share and discuss ‘Benevolent Leadership’. The managerial aptitude of a person can be evaluated according to two criteria: The satisfact...
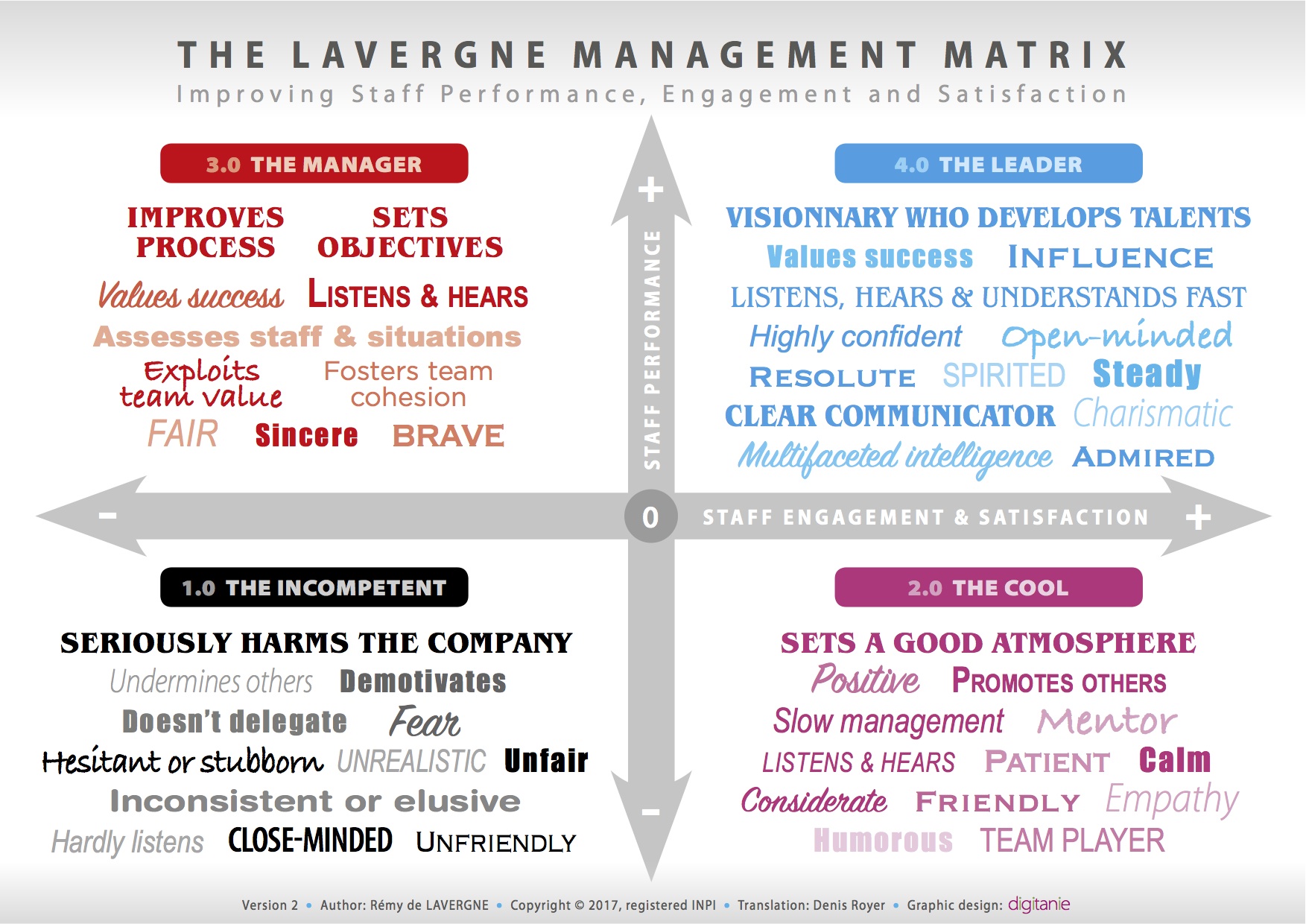
I created the Lavergne Management Matrix to make it possible to share and discuss ‘Benevolent Leadership’. The managerial aptitude of a person can be evaluated according to two criteria: The satisfact...
If you have heard a lot about blockchain but don't really know what it is, you're not alone. The success of Bitcoin and other cryptocurrencies has given blockchain a major leap forward. But cryptocurr...
Have you ever wondered what other company’s fleets look like? How other companies source their fleet units, parts, and services? What information is needed to begin? The first thing to know, is that n...
Sourcing managers with a Microsoft enterprise agreement (EA) that is about to expire face an important decision and may have many questions. Should they renew their next EA along the same lines as the...
The ‘app boom’ is widely recognized to be slowing as we approach the half way mark of 2017. Success stories such as Snapchat and Uber remain (in terms of continued, steep growth), but the aggregate gr...
3D printing and its applications are evolving rapidly, although most manufacturing businesses are at least five years away from mainstream adoption of the technology. It has a long way to go before be...
Organizations that are not leveraging a managed service provider (MSP) and vendor management system (VMS) may be paying too much for contingent talent and are at risk of noncompliance with various lab...
“We take a buck, we shoot it full of steroids and we call it leverage.” -Gordon Gecko (Wall Street 2) Leverage - a word that has such meaning it could be used to define itself. When it co...
Each purchasing category, whether indirect or direct, has a unique set of parameters that can be optimized to take full advantage the savings opportunities in the market. The packaging category is no ...
Design – a term that dates back to the 14th century - has become mainstream over the last decade. Design has done well operating on the fringes of organizations and people are now seeing the value tha...
As I mentioned in Achieving World-Class Procurement Part 1, today’s increasingly competitive market landscape is driving organizations to reinvest in their procurement and strategic sourcing departmen...
Mobile devices are now part of the modern business uniform. Mobile phones created a culture of always available, but mobile devices enable constant connectivity. What telecom companies don’t want CPOs...
Editor’s note: March 8, 2017 has been designated International Women’s Day. This year’s theme: #BeBoldforChange is a call to women in all walks of life to push boundaries and recognize the inspiring w...
In today’s competitive market landscape, simply having a centralized procurement organization is only the first step to better managed supplier relationships and spend. Leading organizations are quick...
Editor’s note: Scott Jancy is a multi-faceted professional, with experience as a historian, an architect, a Naval Officer, a planner, and a consultant. He blogs often on innovation, leadership, and de...
Non-employee talent is getting more and more attention in the executive suite, as contractors, freelancers, and other knowledge-based contingent workers become increasingly important in achieving comp...
Fleet operations can absolutely be an overwhelming category to manage. Between deciding on the right vehicle manufacturer, understanding the ever-changing vehicle features, selecting the appropriate m...
As organizations continue to expand the use of contingent talent to supplement their full-time workforce, they are also seeking ways to optimize their contingent workforce programs to generate additio...
Although we’re a few weeks past the Hanjin Shipping bankruptcy now, the shake up left experts, businessmen, companies, and customers alike wondering what other events could potentially jeopardize thei...
When you just look at a purchase from a pricing perspective, it would be reasonable to think that purchasing products directly from the manufacturer be an effective way to reduce unnecessary overhead ...